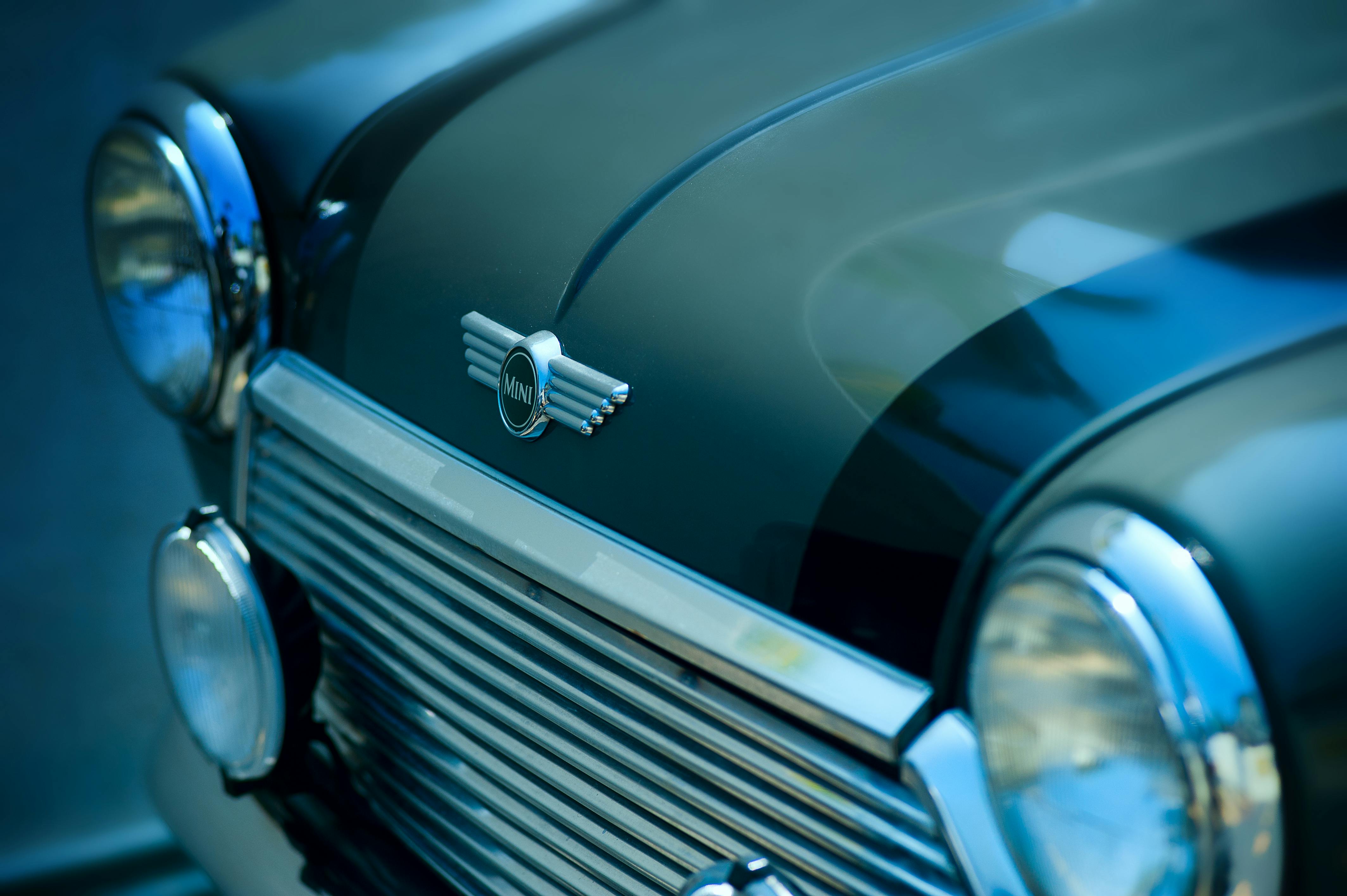
Advantages of aluminum and magnesium wheels for automotive performance in sports and luxury applications
Mark Lisnyansky, president of Magnesium Inc. notes that, “Wheel weight is very important to overall performance as it is a key component in the mass of the” springless “vehicle. In general, the accepted rule of thumb for predicting performance benefits of springs vs. -Spring weight reduction is a factor of approximately 4: 1. For every pound of unsprung mass removed, you get a four times advantage in vehicle performance parameters. For example, magnesium forged, large diameter wheels (20 “-22″) increase the weight advantage over aluminum by eliminating, on average, 70-75 pounds of unsprung mass, which would provide the same benefit in acceleration time. and stopping distance that will remove 250-300 pounds from the vehicle’s engine, chassis, or passenger compartment. ” Lisnyansky goes on to say: “By virtue of these lighter wheels, forged wheels are at least 20% lighter, bear equal loads with better characteristics, which is always easier on the car and its suspension. Lighter wheels too. they produce shorter distance braking, which saves lives, shorter acceleration and reduces fuel consumption. “
The manufacturing process for forged aluminum and magnesium wheels is critical to the strength of the wheels. They are produced by applying extremely high forces to the base material in a contained matrix. Forged wheel blanks, or “blanks,” undergo very beneficial changes in metallurgical grain structure during this process. The more random grain structure found in standard cast wheels becomes a more organized and aligned grain structure when the wheels are forged. More importantly, the metallurgical microstructure of both aluminum and magnesium forged wheels can be further oriented in the forging process to provide the highest material strength exactly where the wheels see the highest load of surface hazards. the road or lateral and other load generated by the inertia of the vehicle itself. Going one step further, today’s advanced computer-aided modeling techniques allow the wheel manufacturer and the automaker to collaborate on optimizing a specific forged wheel geometry and design for maximum strength and safety on the road. the vehicle.
SMW Engineering, a division of Magnesium.com is a leader in the development of magnesium wheels. Magneisum.com engineers recognize that another important characteristic of forged wheels over low pressure cast wheels is the integrity of the surface finish that can be achieved. Most final tire styles and trim combinations are enhanced by the density and uniformity of cosmetic surfaces on forged tires. This is particularly important in high-end vehicle applications where a glossy finish on the wheels is desired, but chrome plating is not an alternative due to mass, cost and environmental considerations. The bright polished and forged wheels certainly make a dramatic addition to the vehicle’s appearance and aesthetics.
While the cost of forging processing is higher than the standard low-pressure casting process used on wheels that come as original equipment on many vehicles, even the most cost-conscious automakers install forged wheels on your highest performing vehicles. By optimizing wheel strength through choice of processes and materials, the many benefits in overall vehicle performance will make forged magnesium wheels one of the key milestones in the next refinement, performance and safety enhancement. of production vehicles.
The technology in the forging of magnesium wheels always advances. With new technologies there are new applications in forging and coating. SMW Engineering and Magnesium.com are regularly researching and testing new design methods. The racing, automotive, and motorcycle world has for some time embraced magnesium wheels as efficient tools for weight reduction, better handling, and increased performance. Luxury car and bicycle manufacturers are now meeting consumer interest and demand for not only high-performance magnesium wheels, but also exclusively designed and coated magnesium wheels.
Magnesium.com recently announced the introduction of one-piece forged magnesium wheels for street use in North America. The wheels are 20 to 30 percent lighter than forged aluminum and offer greater safety and performance.
“The US wheel market is quite formidable and we intend to supply a smaller but very important segment of the 100 million vehicle wheels used in North America,” said Mark Lisnyansky, President of Magnesium .com. “We will provide best-in-class wheels that automakers can offer as an option on new vehicles and consumers can add to their current vehicles.”
Magnesium alloy wheels are initially available in 20 and 22-inch sizes and are treated with a high-tech anti-corrosion coating. The company will also develop wheels in various sizes and compositions for specific North American applications.
“Steel wheels are becoming almost obsolete and the predominant trend is cast aluminum wheels. While most people are not familiar with forged wheels, performance car enthusiasts know that forged wheels offer significant benefits and the forged magnesium wheels, which are lighter and much stronger than their aluminum counterparts, are the next logical step in optimizing vehicle performance. “
Magnesium wheels offer consumers improved safety by shortening stopping distances and offering higher acceleration rates, as well as improving gas mileage. There is also the damping factor of magnesium, which makes it possible to absorb vibrations caused by road imperfections six times more effectively.
Lisnyansky added that, along with safety concerns, “the forged magnesium wheels will also provide a measurable impact on vehicle performance by lowering unsprung mass, an important performance factor.”
Using specialized equipment from the aviation industry, the company has been producing Superbike and Formula One racing wheels for many years. The wheels are forged in Russia by a subsidiary and then machined and finished in Italy.
Why not build a finish line in Russia? “Potential customers, primarily automotive OEMs, often require the comfort level of having their suppliers’ wheels produced locally, even if the forge itself comes from Russia,” Lisnyansky said.
Magnesium.com recently held a “Best New Wheel Design” competition and is in negotiations with several large distributors to establish a joint machining and finishing facility in the US, existing high-end market presence and brand recognition.